7 Questions to Ask a Potential Metal Forging Partner: A Checklist
Choosing a metal forging partner can feel daunting. While assemblers and end product manufacturers have detailed knowledge of their own components, they may lack familiarity with the production process. If you’re not asking the right questions before partnering, it can lead to confusion and inefficiency that will slow you down.
With 100 years of experience, Anchor Harvey sets the industry standard for excellence in aluminum forging. We deliver unmatched quality and precision in every component we produce. Our team places a great emphasis on the value of strong customer relationships and is committed to setting our partners up for success.
That’s why we’ve created this helpful checklist for purchasers, managers, designers, or anyone seeking a metal forging or forge tooling partner. The questions in this article will guide your evaluation of potential forging partners and help you find one that aligns with your standards for quality, efficiency, and mutual success.
Review the questions below and learn why it’s vital to get these answers from any potential metal forging partners.
Table of Contents
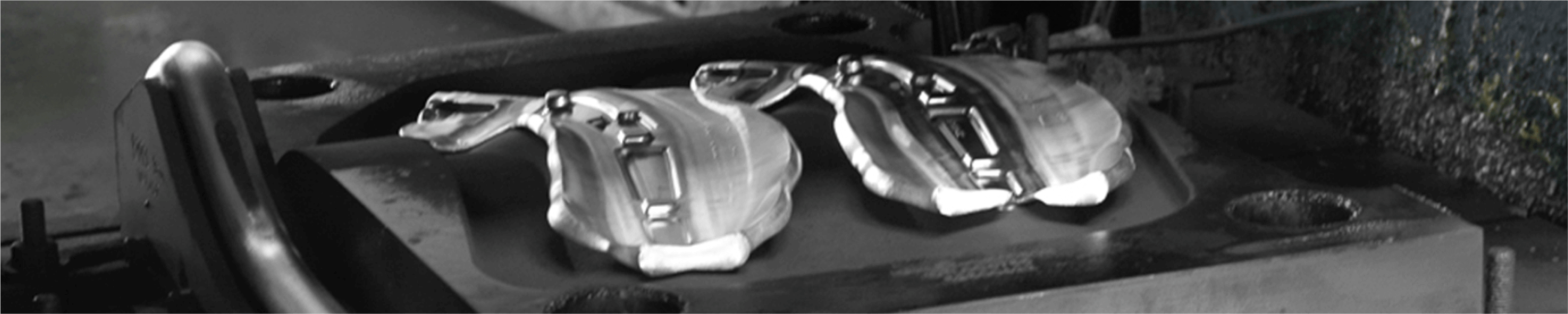
1. What kind of forge tooling services can you provide?
It is vital to establish what a metal forging company is capable of doing, either in-house or through a subcontractor network.
If the parts you need require extremely precise tolerances (e.g. gas-tight housings), it is important to establish the kind of machining capabilities and forge tooling the company can provide.
Anchor Harvey provides a full-service closed-die forging process that produces high-strength, lightweight parts that are suitable for a wide range of applications.
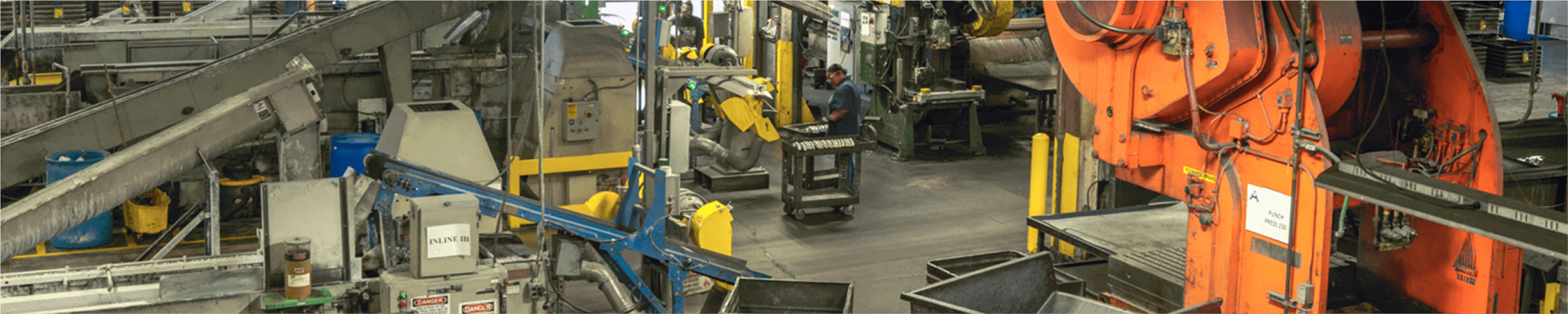
2. What can you do in-house? What is outsourced?
Minimizing cost and lead times are primary concerns for every organization with budgets, but not at the cost of product quality. A full-service shop that provides most processes in-house can promise better turnaround times without the added cost of paying for outsourcing.
Anchor Harvey keeps everything in-house from the initial forging to post-forge machining, heat treatment, and testing. This minimizes downtime during production, which ultimately lowers the price and gets the parts to the customer faster.
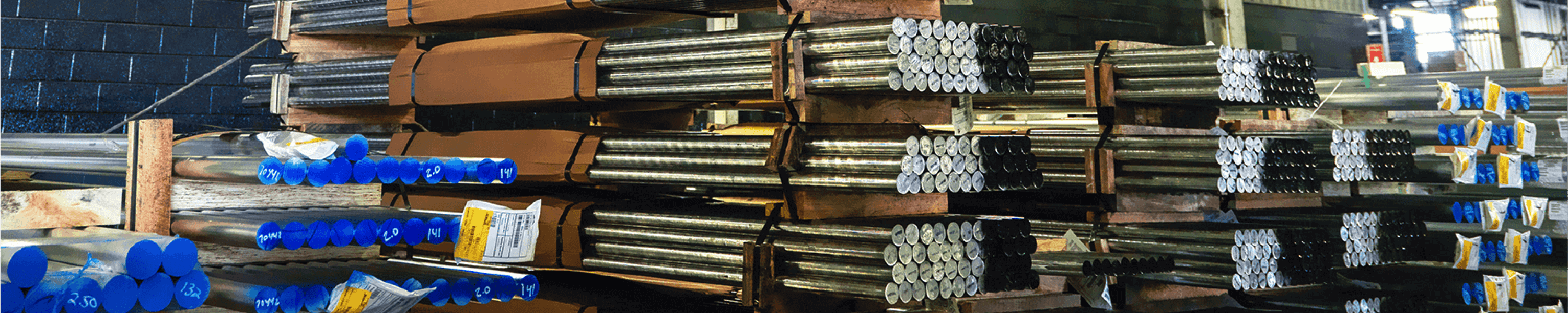
3. What materials do you work with?
Recent advancements in materials science, custom alloy design software, and precise control systems allow for the production of a near-limitless variety of discrete materials to perfectly match the part’s intended use-cases and potential environments. From forge aluminum alloys to magnesium forgings and other materials, there are multiple options to choose from.
Steel, aluminum, and many other common metals are defined by different “series” which are grouped according to common alloying metals and differing ratios of each. Knowing what kind of metals and series that a metal forging company can work with is vital to choosing the right vendor.
Anchor Harvey is an aluminum forging company, specializing in several common series but with the capability to fabricate components out of almost any aluminum alloy series. Forged aluminum, with the right alloying materials, can be made to fit nearly any application, and Anchor Harvey parts can be found in all over the most high-performance sectors like defense and aerospace
Common Forge Aluminum Alloys
7000 Series Aluminum Alloy | 6000 Series Aluminum Alloy | 2000 Series Aluminum Alloy |
---|---|---|
(Aluminum 7075-T6; 7075-T651) Aluminum in the 7000 series is alloyed with zinc to produce the strongest aluminum alloy. Alloys in this series, such as 7075 aluminum, are used for highly stressed structural parts and can be tempered to offer improved stress corrosion and cracking resistance. 7000 series aluminum alloys are commonly used in aerospace and structural applications |
(Aluminum 6061-T6; 6061-T651) The 6000 series alloys combine aluminum, magnesium, and silicon to provide relatively high strength while maintaining a substantial degree of workability with excellent joining characteristics and an exceptional acceptance of applied coatings. Alloys in the 6000 series, such as 6061 aluminum, are among the superior aluminum alloys for use in applications that may require spot welding, fusing, or anodization to provide increased resistance to corrosion. |
(Aluminum 2014-T6; 2014-T651) The 2000 series of aluminum alloys, including alloys such as 2014 aluminum, are “hard alloys” that are commonly used in applications requiring a higher degree of strength or use in elevated temperatures. 2000 series aluminum is alloyed with between 2 and 10% copper to facilitate substantial increases in age hardening and strength. The introduction of copper to aluminum can reduce ductility and corrosion resistance but result in some of the highest strength, heat-treatable aluminum alloy components available. |
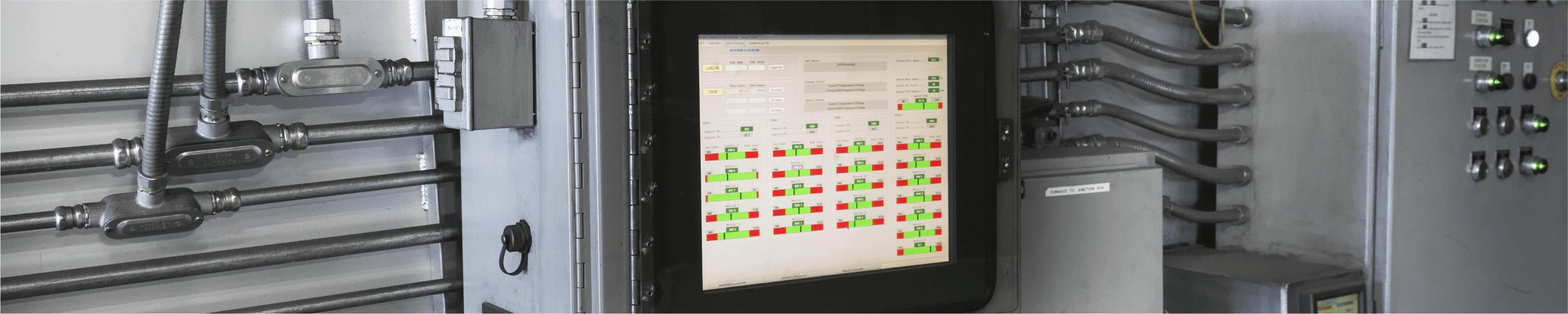
4. What kind of tolerances can you work with?
Every part has tolerances, which are simply the amount of “error” that a fabricator is allowed to make without compromising the performance of the final part.
While it is not possible to make every part perfect to the desired dimensions, understanding process variation and process controls is key to producing parts suitable for high-performance environments – such as aerospace control systems – that naturally demand extremely tight tolerances. Understanding the capabilities that a metal forging company can meet will determine if they are a good vendor.
Anchor Harvey uses exclusively closed-die forges and hosts a machine shop in-house. Closed-die metal forging can hold tolerances that would be impossible in an open-die forge or via drop-forging, and any part with tolerances that cannot be met via forging alone can be refined during machining. With these capabilities, Anchor Harvey can offer the promise of consistently tight tolerances and high-quality products, making them a vendor of choice for any precision application.

5. What are your testing processes?
Every production process has the potential for faults. There are innumerable factors that determine the quality of a part once it exits the production line. Quality production lines can minimize the potential for faulty parts, but some pieces will inevitably be sub-par. To ensure that these failed parts do not end up in a shipment to the customer, a quality metal forging company will have a variety of testing methods and accompanying procedures.
As you discuss testing processes with a potential partner for forged aluminum or other forged metal parts, be sure you are familiar with the distinction between destructive testing and non-destructive testing:
- Destructive testing refers to any method that partially destroys or alters a part in such a way that it cannot be included in your final production batch. In general, destructive testing is used in large production runs where a randomly selected part is representative of the entire batch, and losing the selected part is not cost-prohibitive.
- Non-Destructive testing methods, in contrast, do not damage or alter parts. The tested part can still be usable in the final production run. These methods of testing are important for very small batches or components that are very expensive to produce. Non-destructive testing is especially vital when a single large part is ordered and must maintain its integrity upon delivery.
Various destructive and non-destructive testing processes can range from simple hardness tests and tensile strength tests to CMM (coordinate measuring machine), 3D scanning, ultrasounds, and even chemical exposure tests.
A metal forging company that offers a variety of testing procedures can provide a more consistent product, and can ensure that those products are able to meet the performance standard required by the intended application.
Anchor Harvey offers a variety of in-house inspection processes, including CMM, hardness tests, 3D scanning, and penetrant testing. Through a network of test shops, Anchor Harvey can also access a huge variety of additional testing methods. With these, Anchor Harvey can guarantee the quality and consistent performance of every production run.
Hardness Testing
Depending upon the hardness scale used (Brinell, Rockwell, Vickers, etc.), various loads are pressed against the part across a small ball or indenting tool for a determined amount of time. The part will deform around the indenting tool, and that distance of indentation is used to calculate the total hardness. This process is destructive in nature
Tensile Testing
Also called tension testing, tensile testing is a process that pulls on both ends of a finished part with immense but controlled force. The part will begin to stretch, deform, and perhaps eventually shatter or tear. The amount of time and amount of force used can be included in calculations to determine tensile strength, shattering points, and maximum elongation of the part. This is considered a destructive process.
CMM
A Coordinate Measuring Machine is a large machine that prods the finished part with special tools called probes that can record their location in 3D space when contacting the surface of a part. A machine programming engineer can create an inspection program that prods the part in various critical locations to check critical dimensions. A CMM can include one or more probes that can simply check critical dimensions or can use enough probes and a complex mount to gather so many data points to visualize a simple model of the part.
Penetrative Scanning
Commonly using ultrasonic or radiographic wave generators, a penetrative test maps the internal structure of the final part at varying levels of detail. These scans can identify obvious defects within the structure of the part and can be compared to other scans to ensure consistency in a batch or consistent quality from production run to production run.
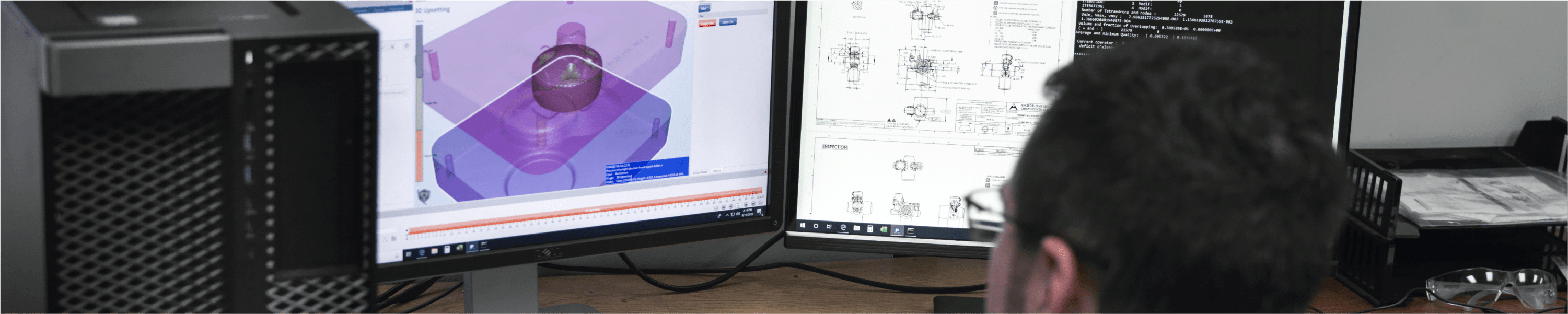
6. Can you provide timeline estimates?
No amount of quality part production will matter if the parts are not delivered on-time. Time to market is critical to ensuring the final potential of a new product, and delay by suppliers can complicate or ruin a release schedule.
Any quality metal forging company will be able to provide at least rough timeline estimates for delivery. A forge tooling company that provides confident and consistent estimates proves that they are experienced with their production line and know their supply chain well.
Anchor Harvey has many decades of experience in the forging business and curates a wide and deep network of vendors that allows them to provide consistent and confident delivery estimates. Alongside short lead times and fast shipping, Anchor Harvey can get parts to customers with minimal delay.
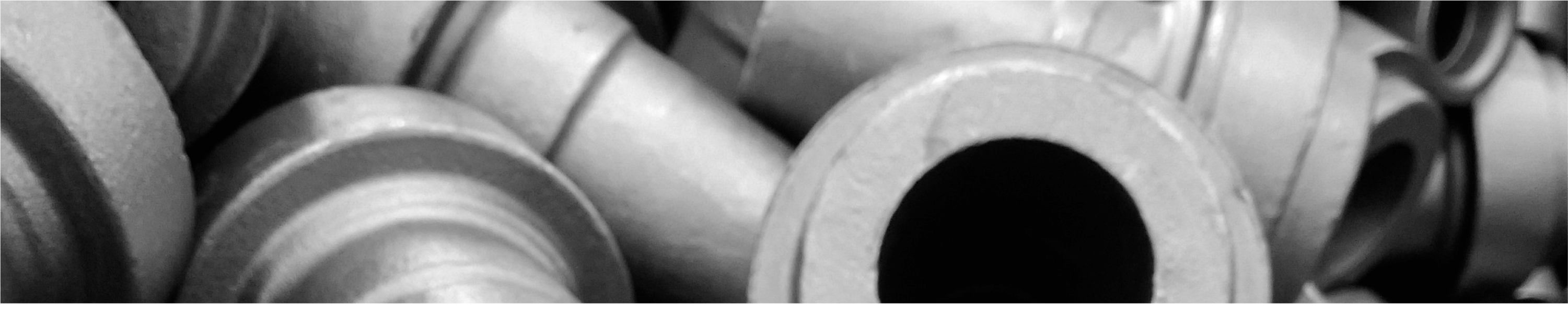
7. What support do you provide for reworking or replacement of defective parts?
If a customer receives bad parts or wants to rework parts without going through the design process again, a metal forging company that provides support for rework or replacement of parts in a timely manner will inevitably be a better partner. Make sure you understand the forge tooling company’s policies for this.
With Anchor Harvey’s fast shipping methods, full-service shop, and guarantee of quality, they can provide generous support for reworking and replacing parts on short notice and in a timely fashion. Anchor Harvey supports its customers through the entire production process, from concept, to production, to delivery, and beyond.
If you’re interested in working with a metal forging partner that has a proven track record, contact Anchor Harvey today!